A new, promising means for producing custom-designed lenses is 3D printing, where the optics can be built through a layer-by-layer deposition of material following a digital design
By Jennifer Taylor, Nadarajah Narendran, Akila Udage, Indika Perera
An essential component of any high-efficiency LED illumination system is its secondary optical system, which is required to transfer the luminous flux of the LEDs to a tailored output beam that can illuminate the target area and meet the application’s light-level and illuminance-distribution requirements. Secondary optical systems use refractive and reflective optical elements to shape the output beam and maximize the total flux transferred from the light source to the application area. In the case of lighting to be used for a specific application, such as illuminating a parking lot, custom optical designs can help achieve required light levels and illuminance distribution at the target area to create good visibility and better user acceptance of the lighted space at the lowest energy demand.
Custom refractive optics (i.e., lenses) provide multiple benefits but creating them with traditional manufacturing methods can be expensive and time-consuming. A new, promising means for producing custom-designed lenses is 3D printing, where the optics can be built through a layer-by-layer deposition of material following a digital design, rather than a subtractive method where the material is cut away or a forming method where the material is formed into shape such as in injection-molded lenses. The building-up process allows for novel designs and shapes that would be difficult to achieve through traditional manufacturing methods.
In recent years, the Lighting Research Center (LRC) at Rensselaer Polytechnic Institute has explored the use of 3D printing to produce custom lenses for use in LED lighting fixtures. These investigations have sought to develop methods for printing optics, optimize designs for custom applications, compare their performance with traditionally manufactured optics and evaluate the long-term performance of the printing materials used.
Methods for printing optics: Several different methods and a variety of materials are available to produce 3D-printed lenses. Of the different printing approaches, vat photopolymerization and material jetting 3D printing processes are the most commonly used in the manufacturing of 3D-printed refractive optics. During these processes, fluid resins either in a vat or jetted onto a surface are converted into solid polymer chains through a photopolymerization process.
Typically in the vat photopolymerization process, which includes both stereolithography and digital light projection technologies, a polymer resin is applied in a layer and then hardened with a laser or a mask image. With these processes, it is possible to achieve a minimum layer thickness as small as 25 μm. To fabricate refractive optical elements, researchers at the LRC use a method of 3D printing called multi jetting of photocurable polymer resin, which is similar to inkjet printing. During this method, UV-reactive synthetic resin droplets are deposited. The material is cured with UV optical radiation before repeating the same process with the next layer. Multi-jetting 3D printing can achieve a layer thickness as small as 15 μm.
When creating 3D models with overhanging structures, 3D printers use either the same build materials or different materials to create support structures. Even after removing the support structure from the printed model, the contact point of the support structure can introduce surface roughness. Hence, to improve the optical properties of the 3D-printed optical components, it is essential to use post-processing methods such as polishing and/or coating. Additionally, this need for post-processing can be controlled by setting part orientation, support structure generation, and design for 3D printing to minimize the need for support while maintaining design requirements.
Design optimization: Designing and optimizing custom lenses and reflectors requires knowledge of the lighting application requirements, the light source and optical material characteristics, and the initial geometry and surface properties of the lenses. As a first step, ray-tracing studies are conducted in optical design software (e.g., LightTools) to understand the optimum lens parameters that will achieve the desired beam shape for the application. Analyses and an iterative optimization procedure are performed to improve the optical efficiency and the beam distribution of the light transferred from the light source (e.g., an LED package array) to the target area. The designed and refined optical component is then translated into a CAD file for 3D print fabrication.1
With 3D printing, the option to produce novel and complex lens designs is promising. In one recent study, LRC researchers used 3D printing to produce an internal cavity lens structure with a smooth planar outer surface.2 In conventional refractive optical systems, the lens’s outer surface geometries are used to refract the light and shape the output beam distribution. Geometric structures on the lens’s external surfaces are generally difficult to clean and maintain when dust and dirt accumulate, which can decrease the fixture’s light output over time. The LRC investigated the feasibility of using 3D printing to create internal cavity structures with refractive spherical arrays. Such a design would be challenging to create using conventional production methods, but the LRC’s study showed that it is possible to manufacture internal cavity structures through 3D printing that can achieve prescribed illuminance distributions.
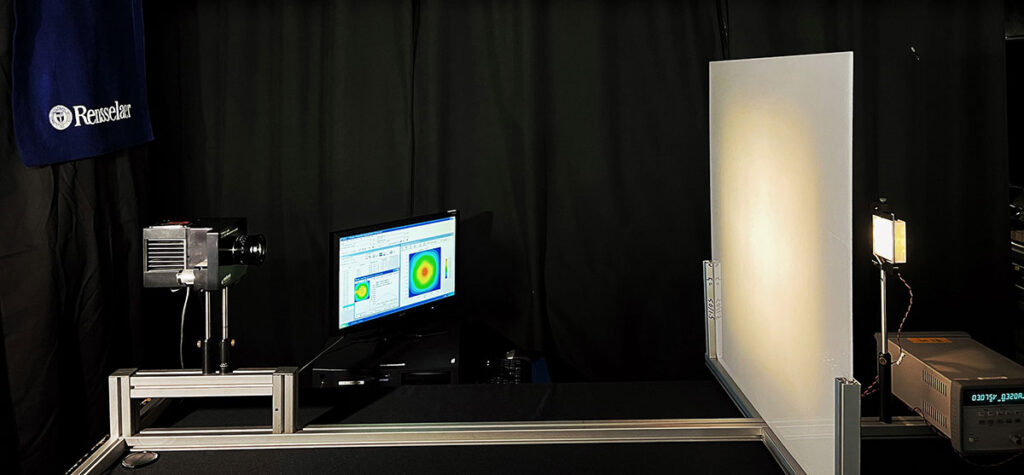
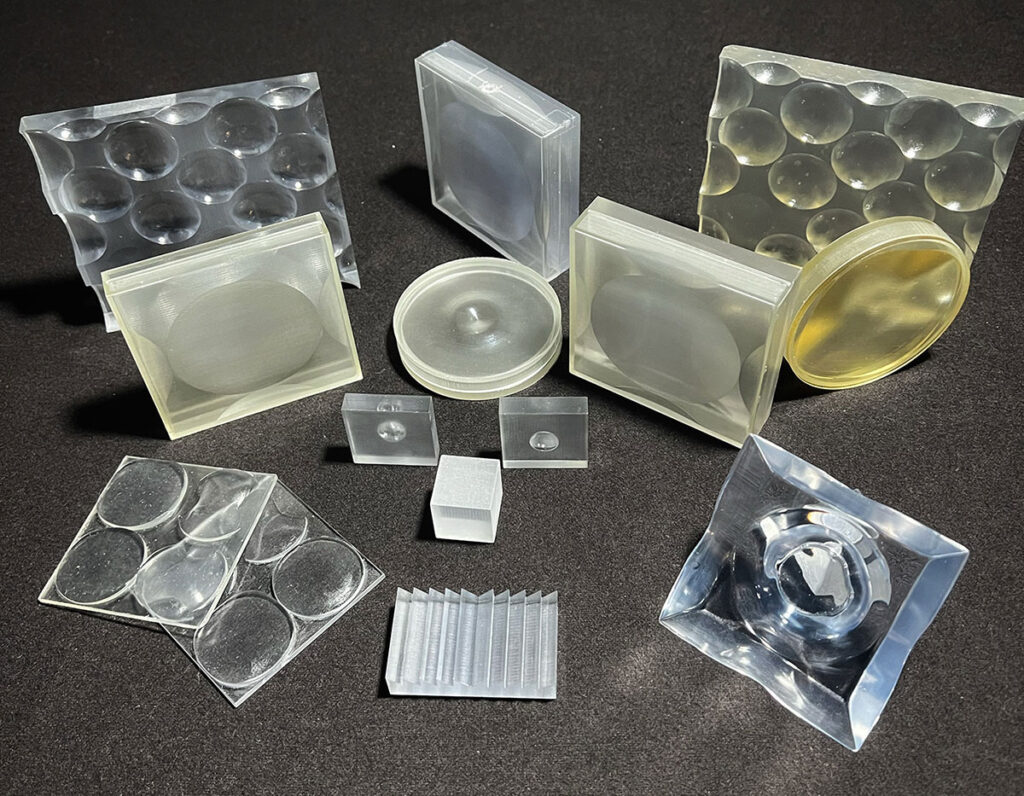
Performance evaluation: In the internal cavity optics study, the lenses were printed using a Stratasys Objet30 Pro Polyjet 3D printer. Post-processing was performed by polishing the surfaces so that the printed lens had high transmission and minimum light scattering. The printed lens was then used in an optical setup (Figure 1) to measure the beam patterns and the total light at the target surface to determine whether the printed lens matched with the raytracing results as a means of validating the design method. A photometrically calibrated CCD camera was used to gather experimental data. In both the internal cavity structure study and in a study where a single refractive lens was designed to achieve multiple beam distributions,3 the LRC found that experiment results matched well with ray-tracing results and predicted optical losses. However, in another study of a different optics design by the LRC, the researchers found disparities between the ray-tracing and experimental results because of a mismatch between the index of refraction used in the ray-tracing simulations with that of the 3D-printed materials.4 Because values like the index of refraction can be different for cured materials compared with values given by manufacturers for raw materials, it is important to pay attention when using such different parameter values in ray-tracing analyses. Still, the results in all three studies provide evidence for the possibility of designing and 3D printing application-specific custom refractive optics (Figure 2).
In a broad sense, the 3D printing of optics offers benefits to lighting applications. Custom designs and print jobs can better match application needs, leading to higher application efficacy. No tooling is needed for low-volume custom manufacturing, potentially making 3D printing cheaper and with shorter lead times. However, studies are needed to understand what types of changes are necessary in optical design software to accommodate for differences between injection-molded lenses compared with 3D-printed lenses with possible interlayer features. We also still do not know much about the long-term performance of the printing materials used for optics and how they will stand up to typical operating and environmental conditions in various lighting applications. The LRC is conducting a new study to investigate this topic, and the results will be published when they become available.
References
1 Perera, I.U., A.S. Udage, N. Narendran, J.P. Freyssinier, and J. Trublowski. 2022. Designing 3D-printed LED optics for optimizing target plane application efficacy. Proc. SPIE 12216, Novel Optical Systems, Methods, and Applications XXV: 122160K (3 October 2022); doi: 10.1117/12.2633620.
2 Udage, A.S., and N. Narendran. 2022. 3D printed internal cavity lens for illumination applications. Proc. SPIE 12216, Novel Optical Systems, Methods, and Applications XXV: 122160L (3 October 2022); doi: 10.1117/12.2641775.
3 Udage, A.S., and N. Narendran. 2022. Achieving multiple beam patterns using 3-D printable lens by altering the positioning of LEDs. Proc. SPIE 12217, Current Developments in Lens Design and Optical Engineering XXIII: 122170H (3 October 2022); doi: 10.1117/12.2633456.
4 Udage, A.S., and N. Narendran. 2022. Optimizing 3D printable refractive spherical arrays for application-specific custom lenses. Proc. SPIE 12216, Novel Optical Systems, Methods, and Applications XXV: 122160H (3 October 2022); doi: 10.1117/12.2632746.