Illuminating NASA’s Next-Generation Spacecraft Systems
Despite science fiction tales of galaxies far, far away, the actual edge of space, known as the Von Karman Line, is only 62 miles above sea level. Hollywood’s depictions of space exploration have historically been presented with excitement and exuberance— “Space: the final frontier” and “To infinity…and beyond!” are just two phrases seared into the public’s collective brain. (And for those who lean more pessimistic: “In space, no one can hear you scream.”) Without effective lighting systems, in space, no one can see you either. As NASA’s Artemis campaign continues to explore the Moon for scientific discovery, technology advancement and to learn how to live and work on another world, it is also preparing for future human missions to Mars. To gauge where NASA stands with illuminating its next-generation spacecraft, LD+A spoke with Toni Clark, Human Health and Performance contract fellow for Spacecraft Lighting Systems (Leidos, Inc.), Johnson Space Center Lighting Lab technical lead, and Extra-Vehicular Activity Human Surface Mobility Program lighting system manager, at NASA Johnson Space Center in Houston, TX.
Can you start by defining “next-generation spacecraft systems?”
Toni Clark: Anything that we are inventing that is planned for space can be considered next-generation. Everything that goes into space is custom—there’s no standardization. It would be nice to have the latest technologies on these spacecrafts but it’s not like Star Trek and Star Wars. You take what you’ve designed for terrestrial applications and then you have to ruggedize it to manage and operate in a spacecraft environment, which obviously is not on Earth. You could even classify high-altitude balloons as spacecraft because you’re at a different pressure, thermal environment and radiation, and all that impacts the successful operation of the electronics that you may want to use. Contrary to popular belief, you don’t usually design the vehicles to look pretty; you design them to survive.
Is the lighting geared toward complementing the overall design of each spacecraft or is the functionality more important than the form?
Clark: Advice is provided to NASA on lighting systems solutions that starts with the standard industry trade recommendations. That includes IES, ASTM, NEMA, the National Highway Safety Administration and many others. You start off with a baseline. Where the application does not fit the design space, as far as these standards, we have to deviate based on the hazards of the operational environment. A lot of times, we start off with a baseline, from a human systems perspective, and then we have to go with human-in-the-loop testing to figure out if we’re allowed to do it differently. When it comes to adjusting how we do things, priority is given to operational safety, performance, crew and system health as well as mission objectives.
From a lighting perspective, you’re probably thinking about how people use light, but one of the major users of light for NASA is camera systems. We have to think a lot about the proper marriage of lighting environments for people and cameras. Sometimes our solutions are bounded by physical architecture for the lighting support systems, including power, radiation, thermal and mass. For example, the IES may recommend 350 lux for a particular application but we may be power constrained and not able to pull off the uniformity ratio recommended for that task because of lamp placement. Then you have to have a tradeoff—are there hazards or productivity issues? Glare, circadian lighting, color fidelity and surface reflectance are all important, and you have to try and find a happy medium.
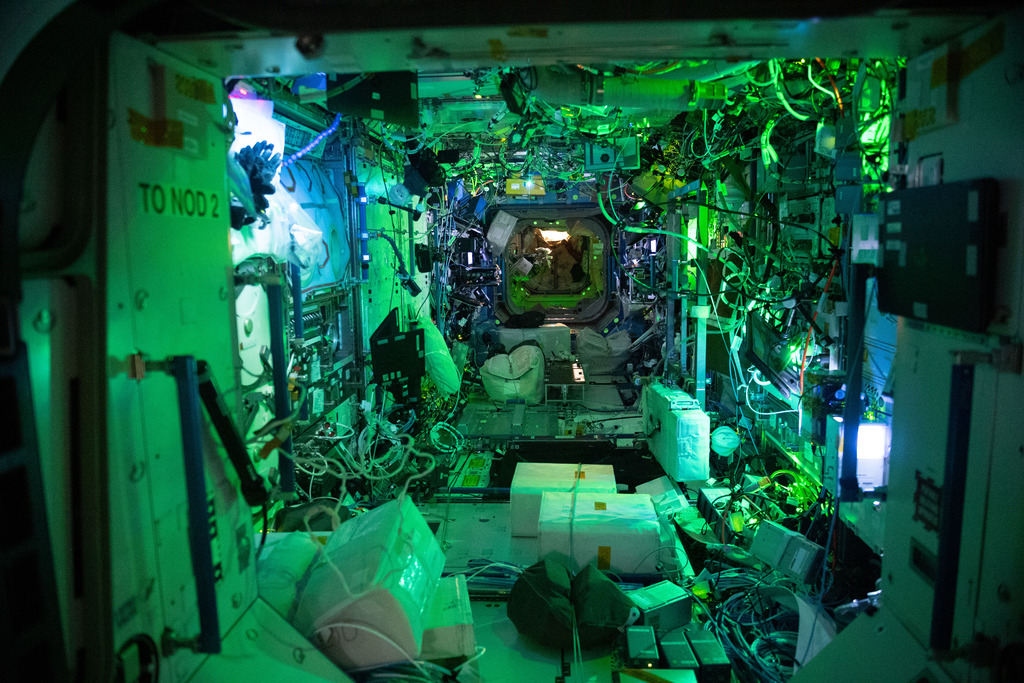
What are some of the most significant challenges?
Clark: The biggest challenge in lighting is the technology—the actual fabrication of the lamps. Companies are now beginning to have their “Aha—light can look like anything” moment. In the hardware world, where a lamp is a lamp, it’s a big leap to try and craft a lamp specification for a light source on a spacecraft that doesn’t look like a light. For instance, can you get away with indirect lighting or having luminous candles where the walls glow? Getting that type of information communicated in a requirement space without being overly prescriptive is challenging. You’re hoping that the person on the other side is a creative individual who sees that and can work with it. In the architecture and lighting worlds, there are many lighting engineers; in the NASA world, there are not. Many times, creativity equals dollar signs. You can have a creative person who comes with an artistic lighting plan and then is told it’s too expensive.
The hardware side is a significant challenge, especially heat. LEDs can burn out rather quickly, so you really have to have a good heat sink design. For spacecraft, they deal with lower gravity, and lower-gravity tasks have challenges with the utilization of conduction to move heat. You need passive conduction or active cooling—and active cooling doesn’t always mean fans. If you’re in a confined space, the last thing you want is another noisemaker. It would be awesome to have a whole IoT system that could do everything. But smart things tend to get eaten up by radiation. All electronics are susceptible to radiation, and memory chips are the most vulnerable. This creates challenges in implementing sophisticated lighting automation systems that might rely on memory or firmware to facilitate automatic actuation.
Materials present another challenge. In a confined space, you have a higher oxygen content, so all of the materials that you’re normally used to dealing with— like plastics, which are highly flammable—have to go through a certification process. You could even have issues with soldering, as certain types of solder processes will grow crystals in space on your circuit board, which can short out a system.
Power is also a limited resource. You have power for your primary systems and your emergency systems and then you have to prioritize what is on emergency systems. In a building, if you have an emergency— the lights go out or there’s a fire—you’re on reduced power that illuminates the escape routes. On a spacecraft, you don’t always get a chance to escape. Sometimes you have to stay and keep things going until a repair can be made. You have to think about contingencies.
Lighting has been improved at NASA with automation, alternate light source designs, enhanced energy efficiency and reduced heat emissions but you have all of these additional electronics issues that affect lamp survival. Getting that thermal, radiation and power trifecta is often a killer on a lot of lamp designs.
How are lighting requirements different between low Earth orbit missions to those on the Moon and Mars?
Clark: Low Earth orbit, like on the International Space Station (ISS), benefit from an approximately 90-minute orbit that provides both daylit and night-time conditions. The spacecraft is close to Earth, and Earth creates a giant diffuse reflector. ISS has both direct high-intensity collimated light from the Sun and intense diffuse light from Earth. From an exterior operations perspective, you have a lot of options. If you didn’t plan your exterior operation correctly, you can just wait for the Sun to come back into a good position—the 90-minute wait is not that bad.
The big impact on lighting design focuses on exterior operations. Let’s talk about leaving low Earth orbit. For example, on the lunar surface, we don’t have a giant Earth hanging over our head anymore; all we have is the Sun. Exterior tasks, especially at the lunar south pole, which is where NASA’s Artemis mission is going, is challenging. The day/night cycle is one month. So, on a one-Earth-day excursion, the Sun is not going to move around much. Whatever is poorly lit, is poorly lit for a long time. This cycle may have some adjustments depending on the rotation/axis of the Moon with respect to the Sun. At the poles, the Sun is coming in at a low inclination angle, which results in the Sun being in your eyes or creating extremely long shadows. On the Moon, the sky is black and not diffuse; there’s no atmosphere or scattered light. Shadows have hard edges and are super-dark—they can be so dark that they look like lakes. It’s like “all-or-nothing” conditions. The visual contrast problem is extreme; you have human eye adaptations and limitations, where you can’t just go from light to dark. If you’re trying to look into a shadow, it’s not a perfect scenario because your eye is still exposed to other objects in the field of view that are not in shadows. Trying to get enough energy into an area to see it is a design challenge.
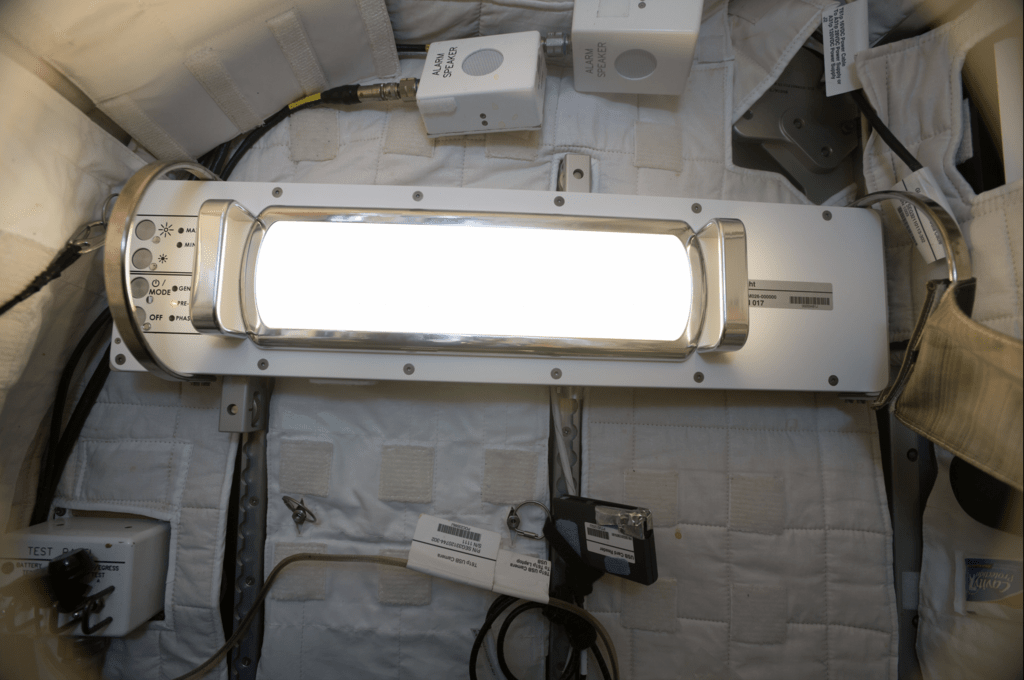
Going farther than the Moon—let’s talk about Mars.
Clark: I haven’t been involved in Mars-specific lighting design evaluations, however, given that Mars has an atmosphere and a day/night cycle that approximately matches Earth’s, my assumption is that standard exterior design processes and techniques would work on Mars but the planet would still present many of the same challenges as does the Moon—addressing weight, radiation, thermal and power.
What research and/or innovations has NASA made thus far to address the lighting needs for future lunar and Mars missions?
Clark: One caveat is that developing something new is very difficult. However, the same lighting innovations that make life better on Earth have the potential to make lighting better for NASA’s purposes. One technology is the Internet of Things (IoT)—how you use communications to improve, wireless or otherwise, the automation of lighting systems, sophisticated communication, actuation of lights turning on and off and smart adaptive systems. Potentially, you may see IoT on a kit that you might be able to certify to allow your lighting system to be more versatile.
I like a lot of the innovations I’ve seen on optical light guides, especially when it could possibly meet the requirements of our materials engineers. It would allow you to have a lamp architecture that fits within the constraints of the physical architecture where the light might go. Let’s say that one of your problems is heat management. An optical light guide would allow you to put the light engine in one place and have the light exit somewhere else, where, from a mechanical design perspective, you couldn’t have done it otherwise. I also like some of the new technology around clear, transparent optical encapsulants. While its use could make a lamp heavier, it could be potentially used for heat management by filling it into the cavity of the lamp to make it more resilient to vibration or dust.
When I look at the automotive world, I like what I’m seeing with solid-state light sources. For instance, several years ago, Audi came out with a vehicle that uses laser matrix head beams, and that was pretty slick. There’s some potential for that type of technology. Some of the companies out there are making holographic diffusers, which is great from a beam-shaping perspective. All of the applications of spectral lighting—there’s now so many types out there including ultraviolet, violet, near-infrared, 800 nm—that you can come up with a very custom spectrum. These all have potential use cases for interior and exterior lighting systems.
Are there any spacecraft that are either new or soon to be unveiled that will integrate some of these technologies? Or are these breakthroughs way down the road?
Clark: NASA has requirements on the books for some of its newer spacecraft for automated lighting systems. They are not in the air yet—so we’ll have to see. This all goes back to the balance of certification; if something is too difficult to certify, you start having to simplify. If it’s not in the requirement space and there’s no business model to have that type of crazy-cool lighting system, you’re not going to see it because the cost of manufacturing for spacecraft applications is so high. Somebody has to have a deep wallet.
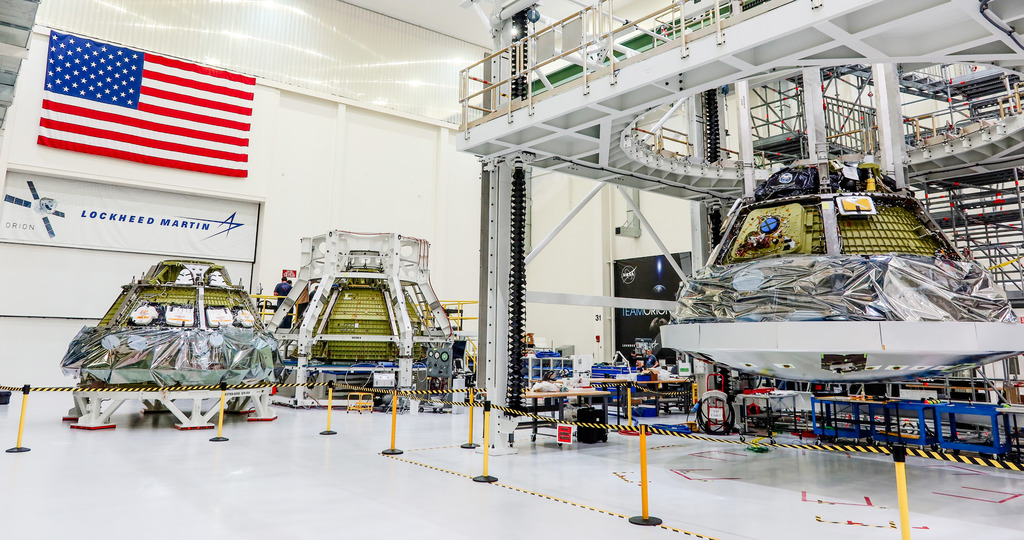
What areas of innovation do you see breaking through in the next decade? Are there any areas that have thus far fallen short of expectations?
Clark: The application of whitelight-emitting lasers and LED technologies that pre-collimate the light before it exits the chip will be game-changers for both Earth- and NASA-based applications. This enables a range of creative optical manipulation techniques and other smart adaptive lighting design techniques. With pre-collimated, you can start doing a lot with optical management materials; you don’t have to waste space with lenses and reflectors to get the light collimated. It will allow for the lights to be tightly matrixed. The white lasers that I know of have a pretty limited spectrum and color fidelity range, so a lot of work has to happen to make those lasers more applicable to lighting.
I would also like to mention that we’ve been the beneficiary of some great work by lighting professionals and organizations. A few years ago, the IES updated its color fidelities scoring method with IES TM-30 [IES Method for Evaluating Light Source Color Rendition]. With IES TM-30, the standard is robust in providing really good information about calculations. From an evaluation perspective, it allows you to do the science in evaluating slight changes in color- or spectrummixing and how it impacts how material look. Another is the IES and CIE push to standardize circadian health countermeasures. In everything we do at NASA, we have a requirement—there is going to be some standard of evaluation for it. Having research out there that has new information that is relevant to the technologies that are being manufactured today really helps with keeping our spacecraft requirements up to date.
Where have some of the technologies fallen short? IoT and automation. I want to have an automated circadian health countermeasure that does all of the thinking for the crew. In some cases, most crew members would like that, but in other cases, people like to march to their own tune. You can’t force people to be healthy if they don’t want to be. Then, other times, you just can’t have the automation system you want—for spacecraft it’s most likely because you couldn’t certify something or you ran out of budget.
The Deep End of the Pool
The 202-ft long, 102-ft wide and 40-ft deep indoor pool at NASA’s Johnson Space Center’s Neutral Buoyancy Lab (NBL) is one of the world’s largest. The lab is used for mission planning, astronaut training, hardware verification and various aspects of ensuring mission success during spacewalks. In preparation for NASA’s Artemis mission to the Moon’s South Pole, where the Sun resides only a few degrees above the horizon—causing extremely long and dark shadows—lunar lighting conditions were simulated at the NBL.
“A few years ago, the NBL approached us about what they could do to improve their pool,” explained Toni Clark, Human Health and Performance contract fellow for Spacecraft Lighting Systems (Leidos, Inc.), Johnson Space Center Lighting Lab technical lead, and Extra-Vehicular Activity Human Surface Mobility Program lighting system manager, at NASA Johnson Space Center in Houston, TX. “NASA has a phrase, ‘Test like you fly.’ For lunar-based applications, we advised them that they needed to darken the walls of their pool because the lunar landscape is a dark sky. We wanted to make sure that when they are performing tests underwater, the contrast ratio that the test subjects are seeing are more relevant to what they would see on the Moon. NBL also invested in a narrow-beam lighting system to improve its test environment by creating a high-contrast scenario.”
NBL requested information from the lighting industry on solutions for the pool’s high-pressure impact environment but most of the companies that manufactured underwater lighting were not interested in tackling the challenge. According to Clark, NASA’s Lighting Lab emulates 130,000 lux at 5-deg beam dispersion on its test articles—including people. “The goal was to try to get nearly collimated but really high intensity and get that contrast threshold up real high,” she added. As a result, the NBL employed a powerful underwater cinematic lamp— the SeaPar Underwater 1,200-W HMI originally designed for the James Cameron-helmed film The Abyss. At 5600K and able to operate at depths up to 120 ft, the lamp, which received a 1991 Technical Achievement Award from The Academy of Motion Picture Arts and Sciences, perfectly fit NBLs needs.
There are plenty of unique hurdles to overcome when designing a lighting environment in the NBL including the depth; refraction index, transmission and absorption of water; and the blue tint of an underwater environment. “Because of that refraction index, you have air to water, so when you’re underwater, it’s like a mirror,” Clark said. “If you don’t keep your light source way down below the water ceiling, the light is going to hit the surface and bounce back depending on the inclination angle with respect to the surface. You need to map out where you are aiming your lights and manage the overhead lights in the pool area.”
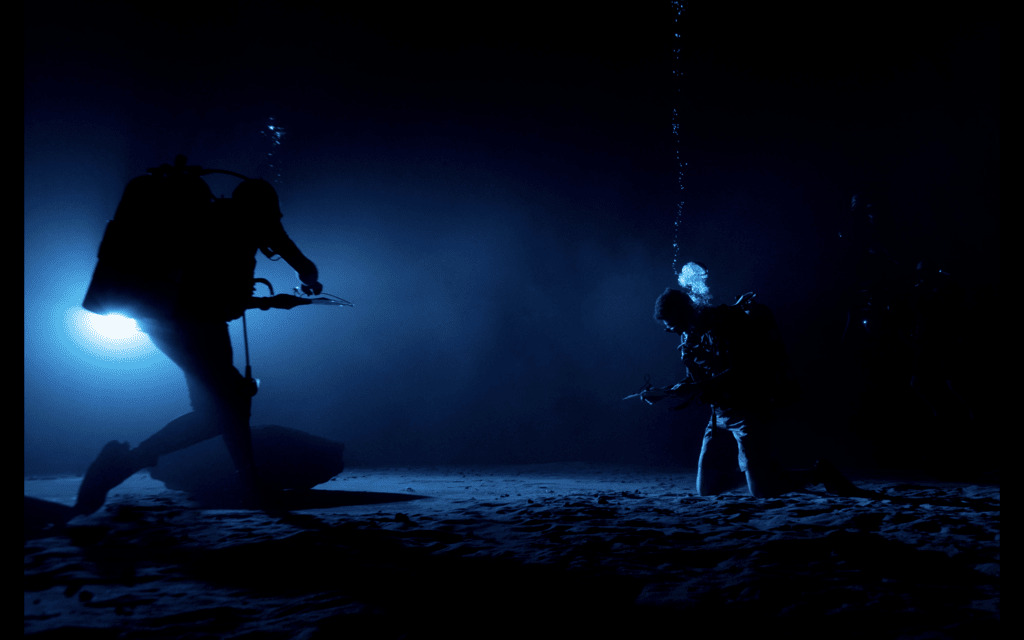